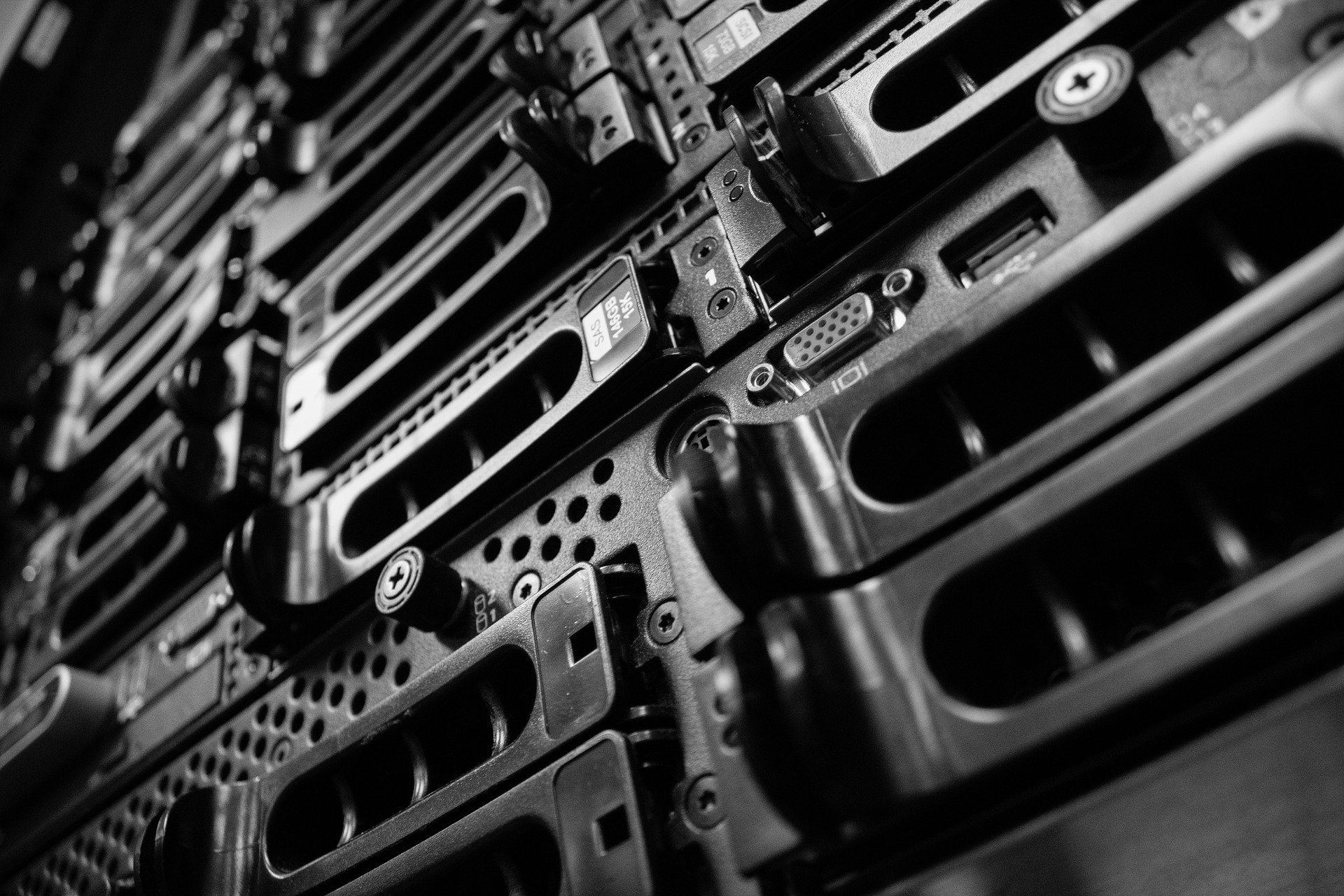
10 Tips for Rack Computer Projects
There is no single approach that can be applied to rack cabinet or rackmount computer projects. Every project is unique, with differing markets, specification levels and demand.
However, there are certain elements that remain the same, and this is the project guidelines –
First, ensure your 19” rack or rackmount computer project has a clear scope, which may include the environmental demands, timeframe and budgets, to understand the exact requirements and reduce risks regarding the initial design phase.
Then, look at the product hardware specification to ensure all stakeholders agree on the activity, specific elements and objectives, before commencing the build phase.
Ensuring each stage of the project is executed to clear guidelines is paramount.
In this blog, we provide some useful tips to ensure your rack cabinet or rackmount computer projects are successfully deployed, on time and within budget.
Tip #1 – Know the Application and Function – (let this define the goal)
To start projects correctly, an understanding of the role the rack system is intended to serve is required.
This will ensure the aspects specific to the customer’s as well as the end-users needs have been considered.
The level of detail does not need to be overly granular: it is not necessary to be an expert in every element and field. However, at the minimum ascertain the must-haves and nice-to-haves from the outset, as these will help to define the scope moving forward.
If the goals are not understood from the outset, the ability to deliver a solution will suffer.
Tip #2 – Environmental Considerations – (think about all potential damaging factors)
Knowing what a solution must provide as a deliverable is only half of the task. It is the overall goal but there are many other obstacles along the way.
One obstacle is imposed by the environment the cabinet will live and operate in. This should be considered as early as possible due to the significant impact it has on product selection and ability to meet reliability and longevity requirements.
The environment has continual effects and therefore must be considered for the entirety of the product life, not just the initial hardware rollout.
If the environment is not one a human would like to sit in or operate within day-in and day-out, there is a reasonable chance that hardware elements will feel the same.
Dust, dirt, rough handling, shock, vibration, heat and humidity all present issues.
Commercial hardware is typically designed to operate in normal operating environments such as offices or homes. When the operation is required outside of this and especially for extended periods, the hardware must reflect the demands of the environment.
Many companies still recommend commercial hardware for these environments and for almost any application. For these companies, their interest is the initial sale and not enduring support issues or elevated TCO.
However, it is not for them to consider the cost of ongoing maintenance, repairs and operating the support team plus additional resources in assumptions or calculations of cost. It is rarely as simple as commercial hardware being cheaper yet still equally applicable.
Typically, it costs less for a reason, and when it does fail it is unlikely to fix itself!
Let customer requirements and the installation environment guide hardware recommendation, not the constant push for a cheaper solution.
Tip #3 – Compliance (ensure it is fit for purpose and certified)
19” Racks often have to perform functions that outlive the individual hardware components as well as meet stringent local or international legislation, ensure this is considered.
At this stage the function the solution is to perform, the environment it must perform it in and under what circumstances is known.
However, how long it has to do it for, or what the in-warranty and out-of-warranty considerations might be may not be known. The operation of a solution must be considered in conjunction with the usable life and costs will be a reflection of this, plus the reliability required.
A computer controlling mood lighting under a bar in a hotel does not perform a critical function and operates in a reasonable environment. It may have a life of several years and the hours of operation may be long but the cost would likely below.
However, compared to a guidance or targeting system for a device with a single operation where the life expectancy could be as low as a minute and reliability are paramount, the same hardware should not be used.
Include compliance constraints with life and environment considerations. These will certainly be required as part of the filter used to identify and validate the suitability of the final product’s specification and Bill of Materials
Tip #4 – Availability and Reliability – (define, agree, prioritise and get clear expectations)
System availability and reliability forms the final pillar of the basic hardware selection framework.
If all foundation project requirements are now understood, this will serve as a good position to make recommendations for the component selection, from a functional perspective, and therefore it is now possible to begin to drive the Bill of Materials (BoM).
This will always bring questions over cost, however, from an engineering perspective, hardware recommendations are typically based on form fit and function first. If the function cannot be fulfilled there is little chance of others remaining relevant, including cost.
Do not underestimate the importance of reliability or availability. Make sure the priorities of both are agreed with the customer and the expectations are defined and quantified.
Tip #5 – Hardware Selection – (choose products that have a good reputation)
Start with what is known; though do not be afraid to look at new technology or products, there is an inherent risk and also cost which can be easily overlooked when laying eyes upon the latest and greatest innovations.
Be wary of marketers promising the solution to woes, gathering compliance information and certification has a cost associated with it. However wonderful they may seem, new products, suppliers and technologies incur cost and timing requirements within their validation.
Hardware should be selected on the basis of what will fit the specific customer requirements best.
Be aware of the budget and alignment with it, but the nuances of spending a penny here and saving a pound there should fall into the remit of an iterative review.
Hardware decisions should be made on imperial data, experience and proven technologies wherever possible.
Tip #6 – Service and Maintenance (be clear on ongoing support options)
Maintenance, servicing and repairs should be quick, simple and easy.
Very often, ongoing servicing and maintenance are overlooked, however, the sale of the product does not stop the moment the solution ships. Good suppliers will offer an ongoing service or maintenance option.
It cannot be emphasised enough that when dealing with integrated 19” racks, the overall operational life of the product should be considered.
Making servicing a simple, quick and easy task, ensures the project is not just successful from the deployment but also ensures it is future-proof.
Tip #7 – Layout and Cabling – (plan routing in advance to define cable lengths)
Cabling is becoming an increasingly essential activity in meeting stringent, safety and EMC legislative compliance requirements.
Effective cabling provides many benefits – it allows data and power to be managed within the cabinet and reduces control issues with regards to signal quality erosion, immunity or emissions.
The ability to distinguish one cable from a large number of others and to be able to re-route or replace it simplifies and accelerates diagnostics allowing for faster fixes and reduced downtime.
Considering the structure and routing in advance wherever possible will help define cable lengths ahead of the build. This de-risk simplifies and reduces the timescale of the build process.
When performing maintenance tasks, well laid out and structured cabling also provides significant benefits.
Tip #8 – Remote Management – (ensure clear requirements for distributed or distanced environments)
Remote management of software and hardware has come a long way over the years.
It now allows for remote updates, firmware loading, soft and hard power cycling, hardware-independent and integrated environmental monitoring, electrical load balancing and automated usage reporting, failure prediction, and reliability analysis. The list is almost endless.
The ability to resolve an issue without attending the site not only saves time but also money.
When beginning to integrate hardware (rackmount PCs) into a rack, it’s important to understand what products are already in place, if any, and how the solution should interact. Compatibility with existing solutions should also be considered.
Many hardware monitoring solutions for UPS, PDU, intrusion, security or environmental monitoring utilise Simple Network Management Protocol (SNMP) and sent traps (messages communicating status information or event activity) can be captured and easily monitored on the network.
Consider that although the majority of SNMP capable devices will be supported under generic Management Information Bases (MIBs) such as MIB-2, many environmental elements may not be covered within this and so are supported by the manufacturer’s custom MIB files.
Accessing or extracting these can often allow third-party software to monitor and sometimes manage the devices. This allows for hardware from a number of different manufacturers to be monitored from a single interface.
Tip #9 – Power – (ensure electrical safety and reliability)
Power is intrinsically important to a 19” rack; electricity is an essential element which rackmount pc’s and equipment would not function without.
From a safety perspective, an understanding of the upstream protection mechanism will be required; ensure that failures within the cabinet can be managed internally.
However, in order to satisfy safety requirements, it may be necessary to confirm that a catastrophic failure of power distribution will trip the upstream protection and that under failure conditions the solution fails safe.
Cabinets requiring a lot of electrical energy often utilise elevated supply ratings of 16A, 32A or 64A and can do so on multiple phases. It is important to remember that voltages and current at play here can be lethal and must never be underestimated.
Always seek prior approval of revised or new electrical designs. Electrical safety inspections and testing should be carried out during implementation as well as on completion of any works, to ensure initial and ongoing user and operator safety.
As a general rule, even when using commercial off the shelf electrical distribution units perform a power budget and validate this during production.
Ensure hardware is appropriately rated for the load and that the load is effectively distributed.
Additionally, certify all devices have power connectivity allocated, the appropriate connectivity type has been confirmed and that any cables required are assessed in terms of their respective ratings and length.
Tip #10 – Cooling – (keep your cool and consider heat waste)
Typically for every 1kW of electricity consumed, 3412.142 BTU of heat will be generated. Therefore, if a cabinet is consuming 8.8kW of energy it will output approximately 30,000 BTU per hour (more than enough to heat the average home when outside conditions are freezing).
All this heat has to go somewhere; traditionally this was considered waste heat and was either distributed to the atmosphere or removed by other means.
To all intents and purposes, every bit of electricity consumed by a computer cabinet is in some way converted to heat and so contributes to both the cabinet’s internal and external environments.
There is increasing pressure to become aware of and manage this waste. This is especially applicable to large installations where a significant amount of energy contained in the heat can be utilised for other purposes or recaptured to reduce the overall electrical energy consumption.
To ensure the operational reliability of the equipment supplied, it is necessary to ensure the data provided for the ambient conditions will remain accurate given the additional contributed thermal load.
With single racks or smaller implementations, it is usually only necessary to consider the direct impact on the cabinet’s equipment and the indirect impact on the room, or cooling system supporting the cabinet.
To learn more about Captec’s rack products or services, visit our 19″ rack cabinets page or our 1u, 2u & 4u rackmount pc’s page.