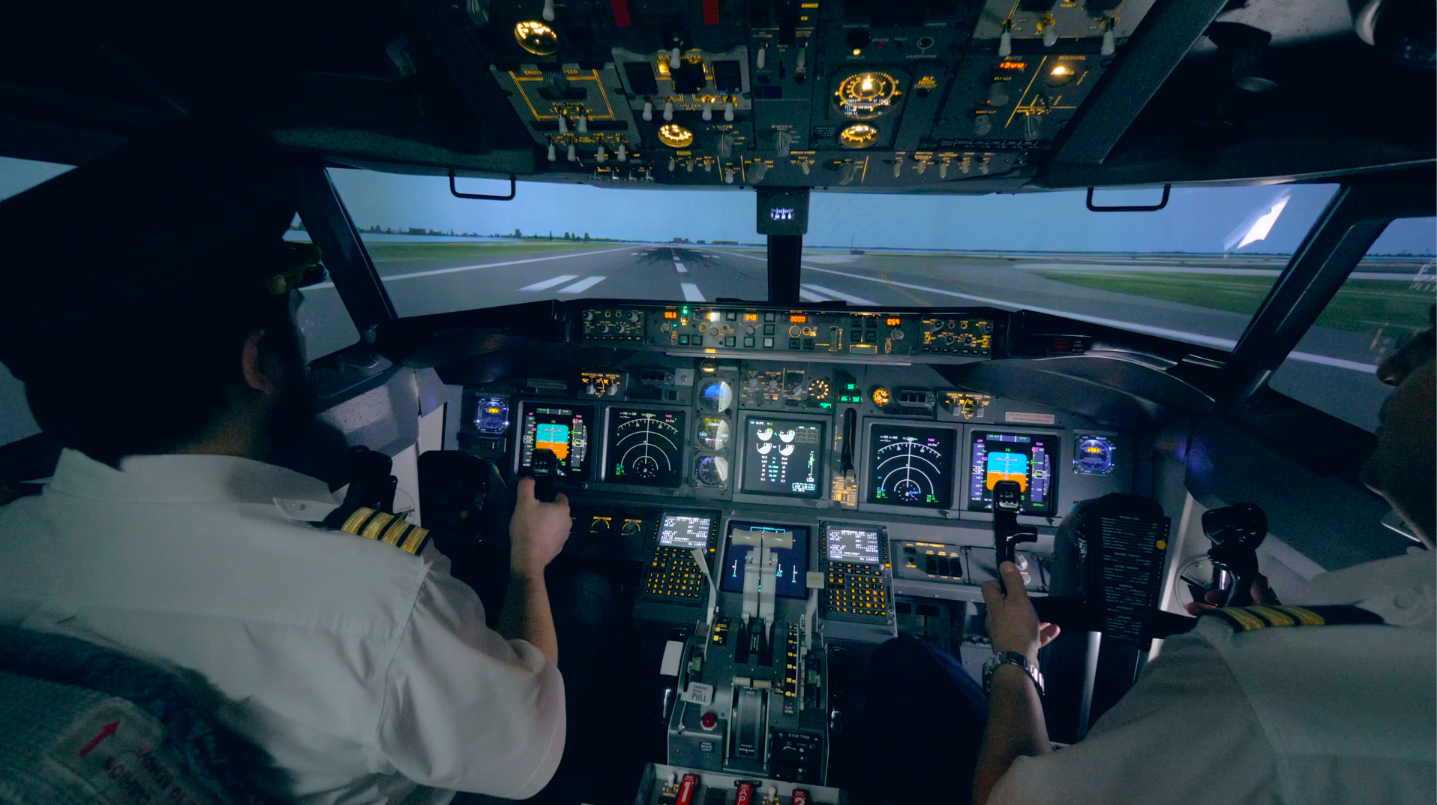
5 Common Flight Simulation Computing Problems and How to Resolve
Simulation applications require high-performance computing and often cutting-edge technology to deliver the best results.
Hi-intensity graphical simulation has the additional challenge of providing an immersive and real-time experience while ensuring minimum latency or data lagging, and using multiple displays or projectors with perfect synchronisation.
Virtual training that provides a real-life environment is essential in the modern world and the more realistic the training feels to the operator the more effective the training experience becomes.
The hardware used is therefore vital and cutting costs on equipment can prove highly prohibitive.
So, what are 5 common simulation hardware problems and how do you solve them?
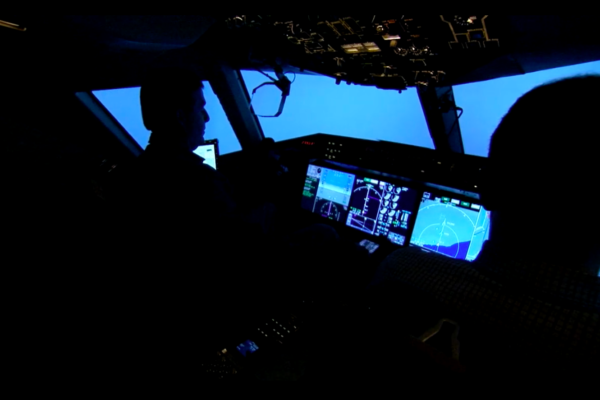
Problem #1 – Performance limitations with compact simulators
Compact simulators are excellent solutions for providing portable and mobile training systems.
Space is often limited on sites and not all training sites can have a permanent simulator, therefore mobile simulators provide the ability to take the training to everywhere it is needed.
However, being portable often forces decisions and compromise on the amount of equipment and also the performance of equipment to be deployed.
To move beyond the performance limitations we need to consolidate functions from multiple computers to a single host and also provide the rendering in a high density, high-performance package.
Problem #2 – Various different hardware components required
Hardware synchronisation costs quickly stack up, the synchronisation cards are specialised and represent a significant part of the investment when considering complex high-fidelity simulation.
Additional cabling may be required for the equipment cabinets and typically each image generating computer requires a dedicated Sync card.
By combining multiple IG systems into a single sub-enclosure we are able to share a single sync card across 4 IG compute subsystems, thus reducing the cost of hardware synchronisation by 75%
Problem #3 – Increased simulator cabinet noise levels
Hi-performance simulators operate at the cutting edge of technology, using the most powerful graphics and processing engines in the market today.
However, all this comes at a cost. Cooling cutting edge power requires huge volumes of air and moving large volumes of air through complex air paths creates significant turbulence and noise. The smaller the area we need to move the air through the greater the noise level created.
In order to provide performance at the cutting edge without the noise levels typically associated with it and without adding huge complexity, cost or scaling up the size of equipment used, we need to redesign out the concept of a computer and design IG and high-end processing platforms with cooling and noise out considered as a major consideration of their design.
Problem #4 – Complex hardware architecture
Reduction in overall architecture complexity become possible and even simple once multiple IG computing systems are consolidated into fewer independent systems. This can either be through virtualisation or for the ultimate in performance through condensing hardware and sharing common hardware components such as chassis, slide rails, hardware synchronisation, cooling systems and power supplies.
Problem #5 – Increased size and weight of simulator racks
By reducing the overall component count within a simulation system you reduce, cost, weight, failure risk, cabling, infrastructure, required cabinet count and overall system volume. This has many benefits, not only in the purchase cost but also in the total cost of ownership.
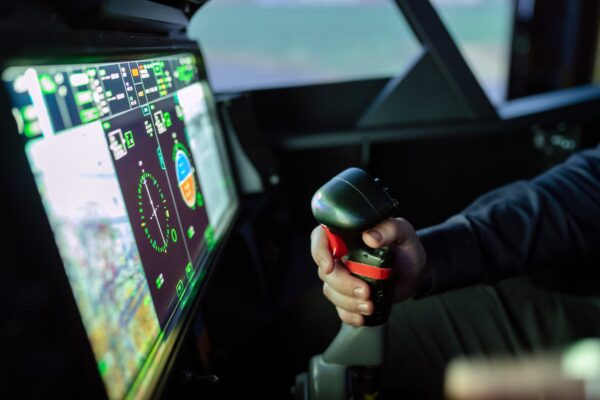
A brand new solution
The Quadbox from Captec has been specifically designed to minimise challenges for Simulator manufacturers.
It maximised performance, minimises noise, reduces hardware synchronisation costs, reduces the overall number of racks and rack space required whilst maximising cooling and reliability.
It is designed to allow for easy field upgrades thus reducing obsolescence risk and allowing the platform as a whole to remain relevant and so reduce both the number and cost of upgrades, as the majority of materials, wiring, chassis, cabinets and associated infrastructure can be retained.
Quadbox has been designed specifically for the simulation market, it targets the needs of the market and is optimised for the equipment operators in this space. A complete departure from the EOM approach where generic platforms with all the complexity and overheads inherent simply have a card or two added.
From the ground up Quadbox is designed to serve the need for high-performance processing and image generation. As a product positioned between platforms from OEM’s and Blade systems, it combines a practical approach to minimise cost whilst maximising performance and reliability.
To learn more visit our Quadbox rackmount computer page, or to learn more about Captec’s full computer range, visit our industrial computers page.
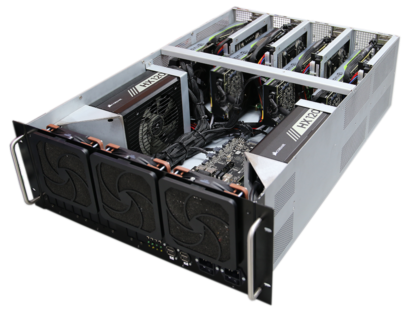