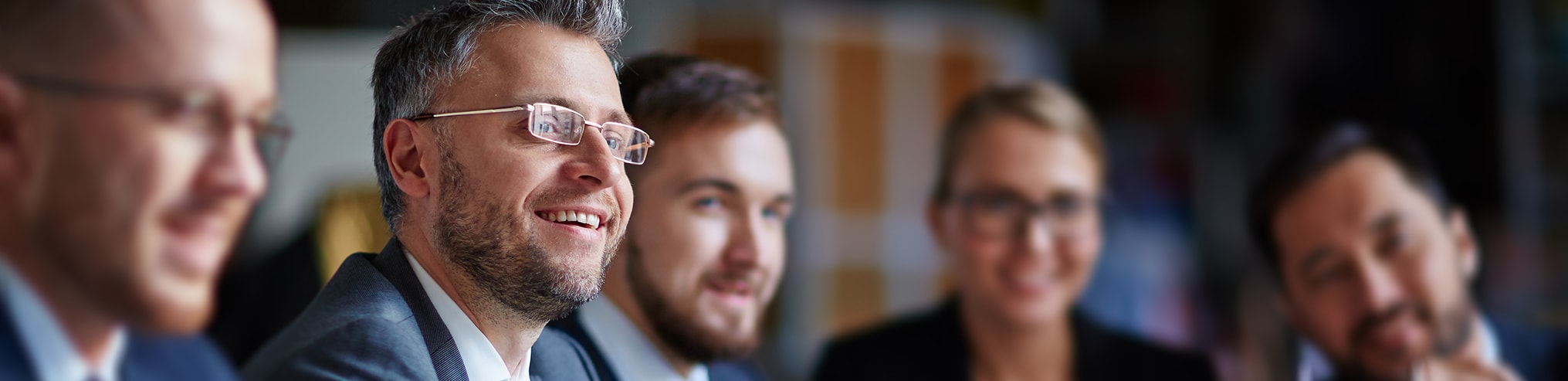
3 benefits of an all-in-one electro-mechanical supplier
The challenge
You may have been there before; a complex project made all the more challenging by the need for a completely bespoke electro-mechanical or box build assembly, often characterised by purchasing teams scrambling to find, set up and approve new additions to their supply chain.
This results in a disproportionate increase of components to purchase as well as a rush to find resource and instructions to build it. All the obstacles that come with a first build of anything.
Maybe it’s a bespoke power distribution unit, a cooling system for a rack or a custom enclosure design to house your own electronic equipment. Whatever it may be, it’s often a necessity to have it manufactured to a bespoke design, rather than buy commercial off-the-shelf.
For some, an undesirable bespoke box build assembly can often feel like unnecessary detail and a considerably higher project management overhead!
A much easier solution is to subcontract those awkward parts out, consolidating a complicated array of drawings, bill of materials and suppliers into a single line on the project, a single purchase order and a firmed up delivery date.
That’s the dream.
What makes a good subcontractor for a bespoke box build assembly?
Beyond the fundamentals of supplier approval criteria set by your own organisation’s best practice and ISO accreditations, the first thing to consider is the mix of services the assembly needs.
A typical box build assembly, by its very nature, comprises of multiple services, such as:
- Procurement
- Project management
- Sheet metal manufacturing
- Painting
- Silk screening
- Wiring
- Assembly
- Testing
- Shipping
So many process steps between multiple suppliers can sometimes be a long way from lean manufacturing with unnecessary waste transitioning between processes.
With this in mind, a supplier that offers all these services themselves – rather than further subcontracting – can be an excellent recipe for success and result in a solution which is greater than the sum of its parts.
3 benefits of an all-in-one electro-mechanical supplier solution
1. Reduced risk
It reduces the potential likelihood of issues arising from miscommunication between your subcontractor and the other companies working with them to supply a secondary process.
For example, problems with a paint finish become a potential project delay where the issue is disputed between the state of the sheet metal before it was painted, and the painting process, rather than a single organisation having oversight of both.
2. Improved efficiency
keeping everything on a single site and supplier keeps the process more efficient.
No time or cost is wasted on logistics and packing as parts move from one supplier to another, both providing advantages to the time it takes to deliver the complete assembly, as well as reducing costs.
3. Holistic view
The final benefit of combining services is in providing another organisation with the big picture of the whole design, allowing them to understand each element fully.
Design optimisation then becomes much more effective. The vendor is able to provide advice on how best to productionise that original prototype design, not just from one point of view, but the entire set of disciplines, and how they might interact differently.
Here’s an example:
Imagine how a small change in sheet metal design with an all-in-one subcontractor might make it quicker, and therefore more cost-effective, to perform the related processes such as painting or assembly further down the line.
This is ideal for an awkward box build assembly making the transition from the initial rough and ready prototype or proof of concept to a completely finished and productionised device.
This also has another crucial benefit – this time, for project managers; this big picture view also helps substantially derisk the transition from prototype or design to realisation.
For the same reasons, understanding the interaction between processes and parts of the design helps you identify potential production issues before they occur, thus reducing the risk of delays, or additional cost down to rework, or worse yet, the complete scrappage of parts.
In summary;
Finding a subcontractor for a difficult bespoke box build assembly that has the services you actually need under one roof can lead to;
- Lower risks
- Faster delivery
- Lower cost per assembly by eliminating waste and dispute in the process.
It will also smooth out the manufacturing process through optimising your design for manufacture with multidisciplinary expertise.
To learn more, visit our electro-mechanical box build assembly and fabrication web page.