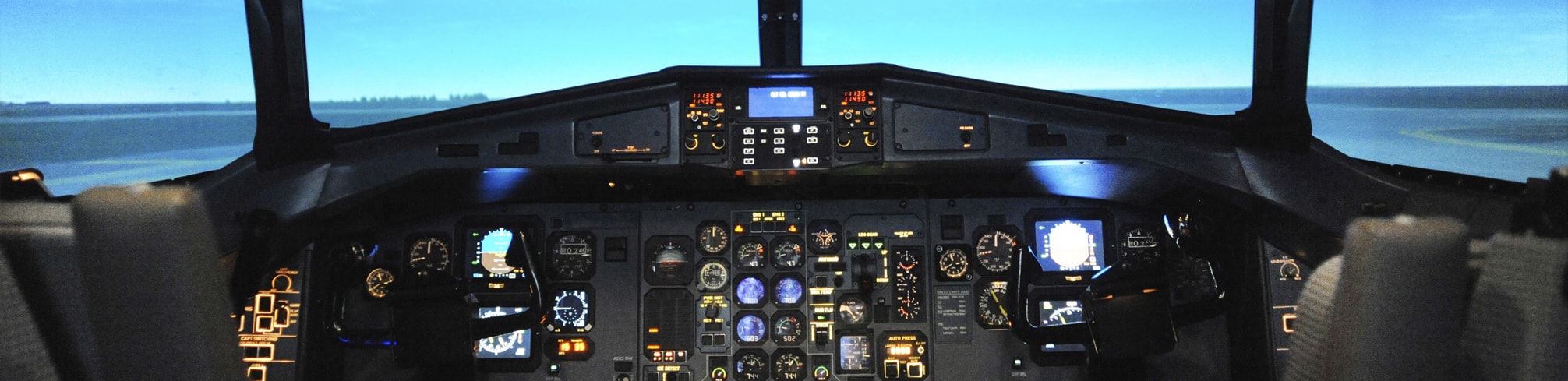
The Evolution of Flight Simulation
Flight Simulation – Past, Present and Future…
April 2018 marks the 100th birthday of the Royal Air Force, and in anticipation I thought we could take a stroll through the archives to look at how flight simulation has evolved. In this blog, I’ll investigate the machines that trained our pilots, highlight significant changes and see how technological advancements helped shaped the future of flight simulation.
The Past
1910 marked the birth of the first non-wind assisted flight simulator. Consisting of a barrel cut in half and a wooden base, it saw one half of the barrel upturned for the pilot to sit on. The “plane” was then manually moved while the pilot attempted to keep line of sight with the horizon. In 1914, the skills of pilots became a priority and this lead to the introduction of equipment designed to record the reaction times of the pilot. Using this equipment, pilots could be assessed and selected for flight.
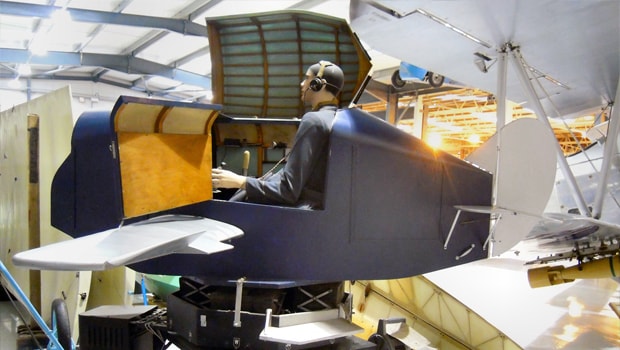
The next major step in flight simulation resulted in the movement of the simulator being directly linked to the pilot control system. Although there were many iterations and steps leading to the introduction of Edwin Link’s 1929 ANT-18 Link Trainer, this is widely known as the most successful simulator of its time. This was a complete trainer. Not only did it re-enact the movements of a plane using a complex set of air-driven bellows connected to a vacuum pump, it was also capable of tracking the potential flight path of the aircraft using a wind drift analogue computer marking its movement onto a map. In the late 30s to early 40s, the D2 model of this was produced and used by the RAF to train their pilots. These were seen as having a pivotal role within the RAF’s pilot training scheme. Following their use, RAF Chief of Staff, Air Marshall Robert Leckie, expressed the importance of the Link Trainer, claiming that battles were won with a squadron of Link Trainer pilots!
The Present
The progression to modern full flight simulators began in the late 1920s with a patent outlining the use of analogue computing to control the dynamic simulation of an airship height control system. It took until the 1940s for analogue computing to make its mark in the simulation industry, with commercial airlines using full aircraft simulators. Although there was no visual system or motion, it had a static cockpit allowing the crew to be trained on flight and emergency procedures.
The 1960s brought with it the introduction of sophisticated motion systems, with vertical motion being added to the pitch, roll and yaw movements. These came in the form of huge structures with complex hydraulic systems which proved very difficult to maintain. These hydraulic systems continue to be used now, but are often substituted with electric motion systems.
In the late 1960s, the introduction of digital simulators paved the way for a quality of immersion so sufficient that in 1979 the FAA published the Advanced Simulation plan amendment to regulation 121. This enabled all training and checking of airline transport pilots via the use of a “qualified” simulator.
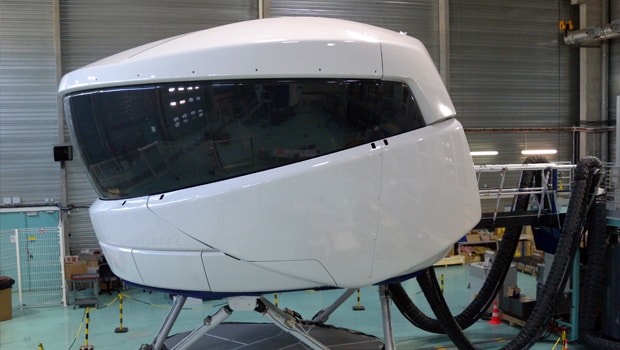
Zero Flight Time Training was quickly established and by the early 1980s, equivalents to modern level D simulators were in production. In 2006, the first full flight simulator with high fidelity electrical motion was awarded Level D certification by the FAA. This was as a result of co-development between Moog and FSI. Advancements within this technology and the utilisation of the ball-screw developed by Moog enabled smooth transitions and highly controlled movement of the cockpit. This resulted in a highly realistic feel for the pilots in training.
With advances in digital computing, we are able to couple the motion with ever-higher resolution graphical projection and displays giving a true out-the-window (OTW) “Geospecific” experience. Products like the electrical 6 axis Reality H from Thales and L3’s simulator platforms couple high fidelity motion tables with realistic OTW, live instructor interaction and exceptional build to enable mission and flight readiness. Pilots can gather many hours of realistic flight experience without hands-on access to an aircraft. The advent of classroom trainers, flat panel and full flight systems mean that demand on high fidelity simulators and aircraft is managed and experience is accrued efficiently and effectively.
The Future
So, where does this leave the future of flight simulation? We are already seeing the development of robotic arm simulators. Allowing the cockpit a much larger range of movement, these are capable of producing G forces equivalent to those experienced inside the aircraft when in flight. This addition is another major step towards the realism of military training, where aircrafts are capable of putting pilots through very high levels of G force.
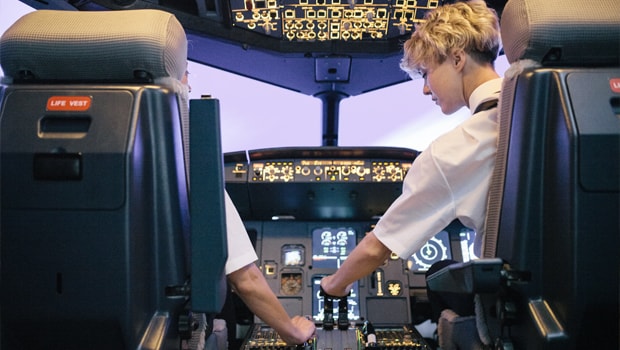
With emerging technologies and the adoption of VR (Virtual Reality) in the computer and serious gaming industry, it is inevitable that technology will progress to ever-more immersive experiences, reducing the need for large and costly projectors and displays. Personally, I think we will see an increase in the use of interchangeable cockpits, reducing the overall cost of ownership and providing a broader training experience capability.
I look forward to seeing where the future of this exciting technology takes us and helping Captec’s many simulation customers achieve their computing ambitions.
If you require design to order rack capabilities contact our specialist team to discuss your next flight simulation solution.