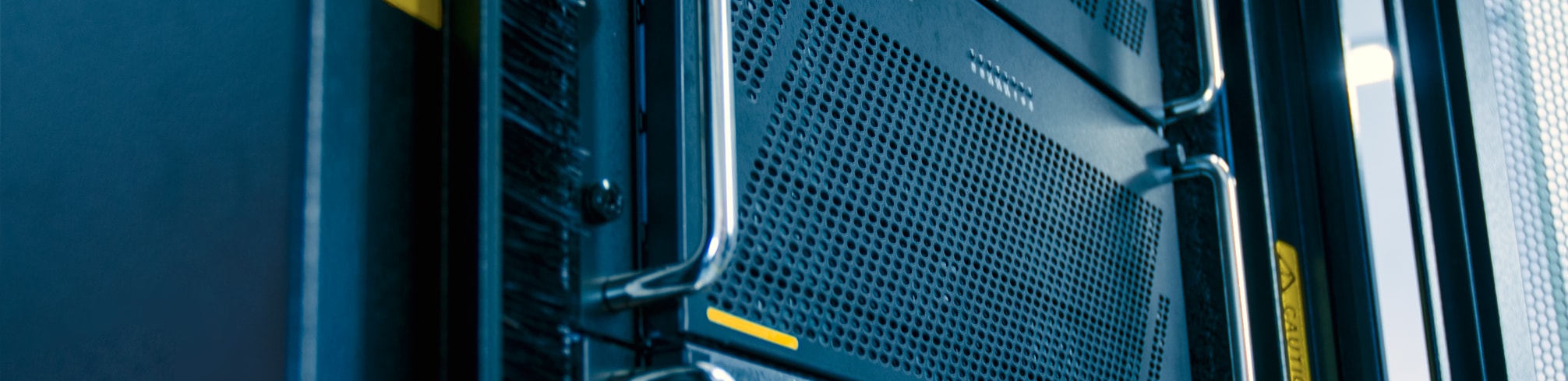
Rack integration: navigating risks for project optimisation
Rack Integration
The demand for fully populated and functional rack cabinets is set to increase in line with the evolution of technology and resultantly, the enhanced capabilities of applications. Designers and engineers competent in rack integration will become an increasingly valuable asset to industry as organisations look to outsource projects due to time, risk and complexity concerns.
Computing platforms and components are constantly increasing in both scale and complexity. This drives the need for businesses to reduce their footprint and increase the density of equipment by way of integrating them into 19-inch rack enclosures. This, in turn, can cause a unique but additional strain on the technical resources of a company.
Sectors most in need of high powered and high performance rack systems include automation, medical and energy but this need is spreading across many more industries. Within these industries, applications are often considered as mission-critical, meaning racks need to be capable of continuous operation and as such must be specified for both reliability and extended longevity.
The process of integration itself is inherently multi-faceted, complex in nature, and has the potential to create a multitude of risks if left in the hands of time pressed engineers with vastly divergent tasks – or worse, a business looking to save a bit of cash by attempting it alone with limited experience.
To optimise 19-inch rack cabinets for success, projects must be considered holistically in order to assess, counteract and mitigate risk factors. After gaining a full understanding of the rack’s intended function and the timescale it must perform this for, it is crucial to perform an onsite assessment to evaluate any challenges imposed by its environment. Considering these aspects before undertaking any design or engineering work plays a big part in ensuring that once the rack is built, any unwanted surprises are reduced to a minimum.
For designers and engineers, a critical part of integration is to pre-empt and understand complexities from the outset of the project. Component selection plays an important part here. Hardware should be selected on the basis of what best fits the individual longevity, projected availability and performance requirements of the application. Components should be recommended based on empirical data, experience and proven technologies wherever possible.
Two of the most crucial aspects of a successful rack design are ensuring it has enough power for continuous operation, and can be efficiently cooled. This will provide assurances that the rack won’t overheat when demand on performance is at its peak. To this end, integrators should perform accurate power and thermal budgets using the performance criteria and knowledge of the operating environment as a starting point. The budget calculations will give a precise calculation as to how much power the rack will need to consume during its operation. It will also define the means of power supply needed within the enclosure and what technologies are best suited to maintaining the optimum temperatures in the overall unit.
The power and thermal budgets will also prove useful in driving mitigation strategies to be put in place in the event that the rack fails, minimising downtime and contributing to the construction of a rack capable of a long, healthy lifecycle. These strategies can include ‘Mean Time to Repair’ (MTTR) and ‘Mean Time Between Failure’ (MTBF) calculations.
This is all just the tip of the iceberg. Designers and engineers must also consider compliance testing, cable layout and management, full build documentation, technology refreshes and so on. Despite the seemingly never ending list of aspects to consider and risk factors to overcome, integrating a rack optimised for reliability is certainly achieved with 360 degree consideration, sagacity, precision and skill.
To learn more, visit our Rack Integration page.